Why FeTu
As tradition has it, in visualising an ‘engine’, ‘pump’, ‘compressor’, ‘turbine’ or ‘expander’; we imagine five discreet machines which all appear and function in very different ways.
But why do they differ when their core need is the same?
‘to convey energy between volumetric and rotational states’.
Possibly they differ on account of running a non-ideal architecture? Each adopting a design methodology which offers the path of least resistance for their given need.
A turbine is a simple, elegant and beautiful solution but suffers on account of not being a positive displacement device.
A combustion engine can reliably deliver torque at low speed on account of being positive displacement, but its complexity and inelegance involves; sliding, lots of lubrication, and the synchronisation of 300 moving parts.
These machines are two-dimensional entities running in a planar fashion around a single axis. Could a 3D motion offer more functionality with less complexity?
So in these Energy-centric & Carbon sensitive times how would we describe an ideal architecture to harmonise these machines for simplicity and efficiency?
- Continuous flow (simultaneous suction & discharge)
- Positive displacement (low speed)
- Compact, lightweight & scalable
- Low friction (non-contact)
- Simple & elegant
Such is FeTu
With the added potential for a closed-loop thermodynamically reversible heat engine.
Uniquely, FeTu employs a single spherical rotor whose three dimensional movement enacts the simultaneous displacement and precise port timing of four discreet, non-contact, positive displacement chambers.
“I have never monitored or witnessed an Innovate UK funded project which has over delivered on expectation by such an amount as this”
Bruce Blackburn, Innovate UK monitoring officer
The system is made up of a single drive-shaft which runs through the device carrying a spherical rotor. The rotation of the shaft causes the rotor to ‘roticulate’™ in 3D space (simultaneously rotate and articulate). The rotor follows a defined path, operating the chambers formed in the space separating the two parts. The chambers are configured in such a way that the inlet and discharge ports each receive continuous flow.
The chambers rotate with the rotor, meaning they spend equal time in the compression and induction phase; this imparts a cooling effect on the internals. The proximity of the chambers as they rotate is local to the inlet during induction and local to the discharge during compression. The design makes it impossible for a chamber to be in communication with both suction and discharge ports at the same time, meaning it can operate normally and effectively in a valveless state.
The dynamic parts do not make contact but run in close proximity, sufficient to effect a seal. The leakage path lengths are long and stagnate flow through them to assist sealing. The only contact points within the device are by means of frictionless bearings.
Uniquely, the FeTu architecture can be built with a different volume chamber on the top and bottom half of the design, allowing the device to act as compressor and expander (Compander)
One Device - Many Applications
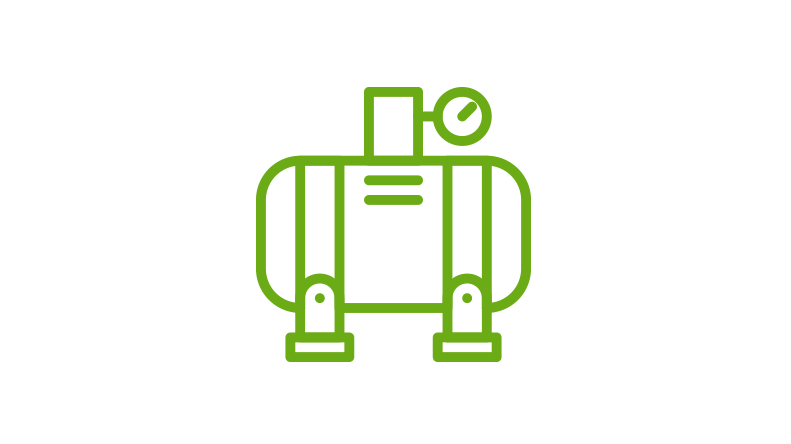
Compressor
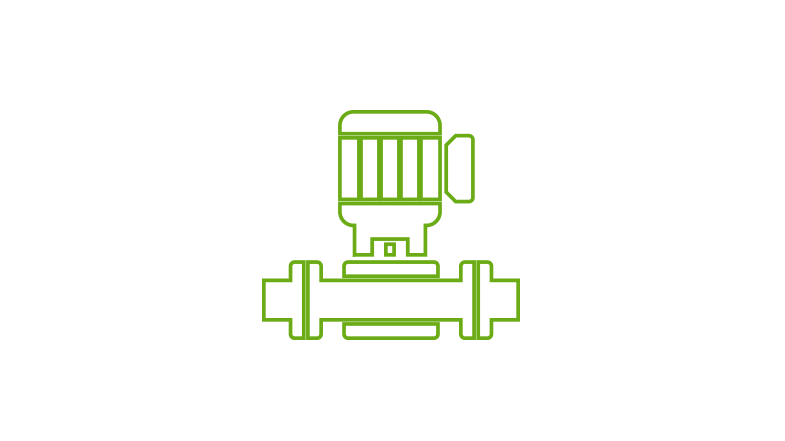
Liquid & Vacuum Pump
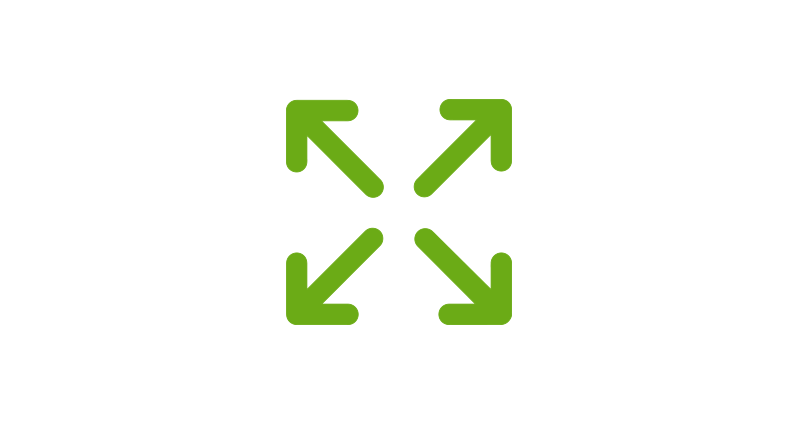
Expander
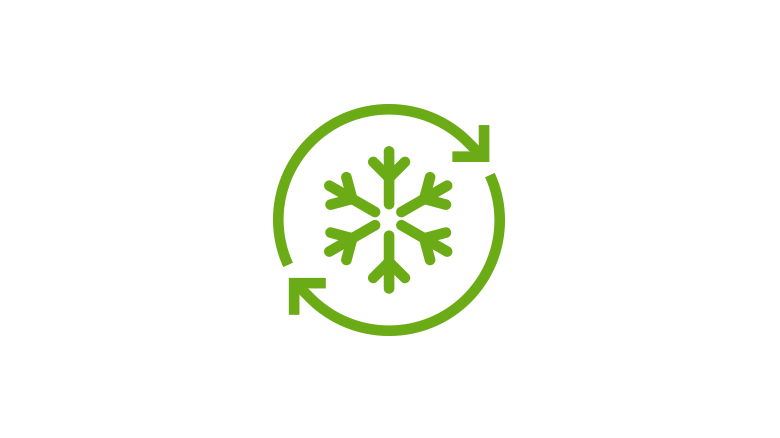
Refrigeration
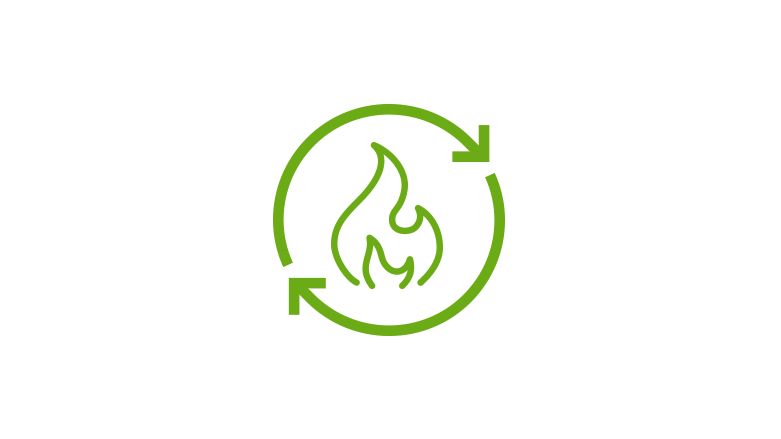
Heat Regeneration
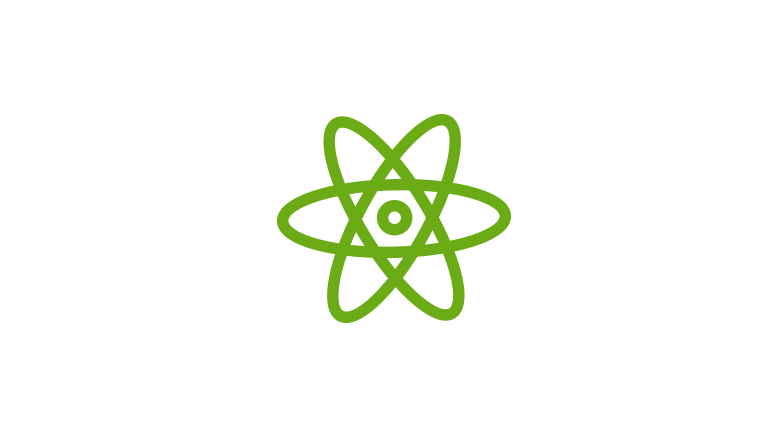