Technology
The FeTu Roticulating System
The FeTu™ Roticulating™ system is a new and entirely novel energy architecture targeting mass cross-sector decarbonisation. This ‘Positive Displacement Low-Velocity Turbine’ (PDLVT) combines the finest characteristics of radial, axial and reciprocal techniques into a single high-efficiency solution.
Its beautiful elegance uses one part to control a single spherical rotor which moves in 3D space enabling precise & simultaneous management of four volumetric chambers. With only one of its ‘two moving part’ design defining chamber movement, it is perceived as the world’s first ‘quad-acting’ (duplex double-acting) device, offering four discreet chambers defined by a single set of mechanical constraints.
Translating energy seamlessly and continuously between rotational and volumetric sources, FeTu has applications in power generation, pumping, compressing, expanding and thermal propulsion. Akin to a human heart, the unique twin-suction + twin-discharge design allows duplicate or differential activities. Pressure or flow is managed within the same unit, which also provisions a closed-loop Green Energy harvesting platform with a high degree of thermal reversibility; an idealised principle perceived by many as the key to unlocking large-scale sustainable energy from solar and geothermal heat sources. Open-loop capability also offers efficient and clean portable power generation to overcome range anxiety and ‘on the fly’ recharging of electric vehicles and mobile transport systems.
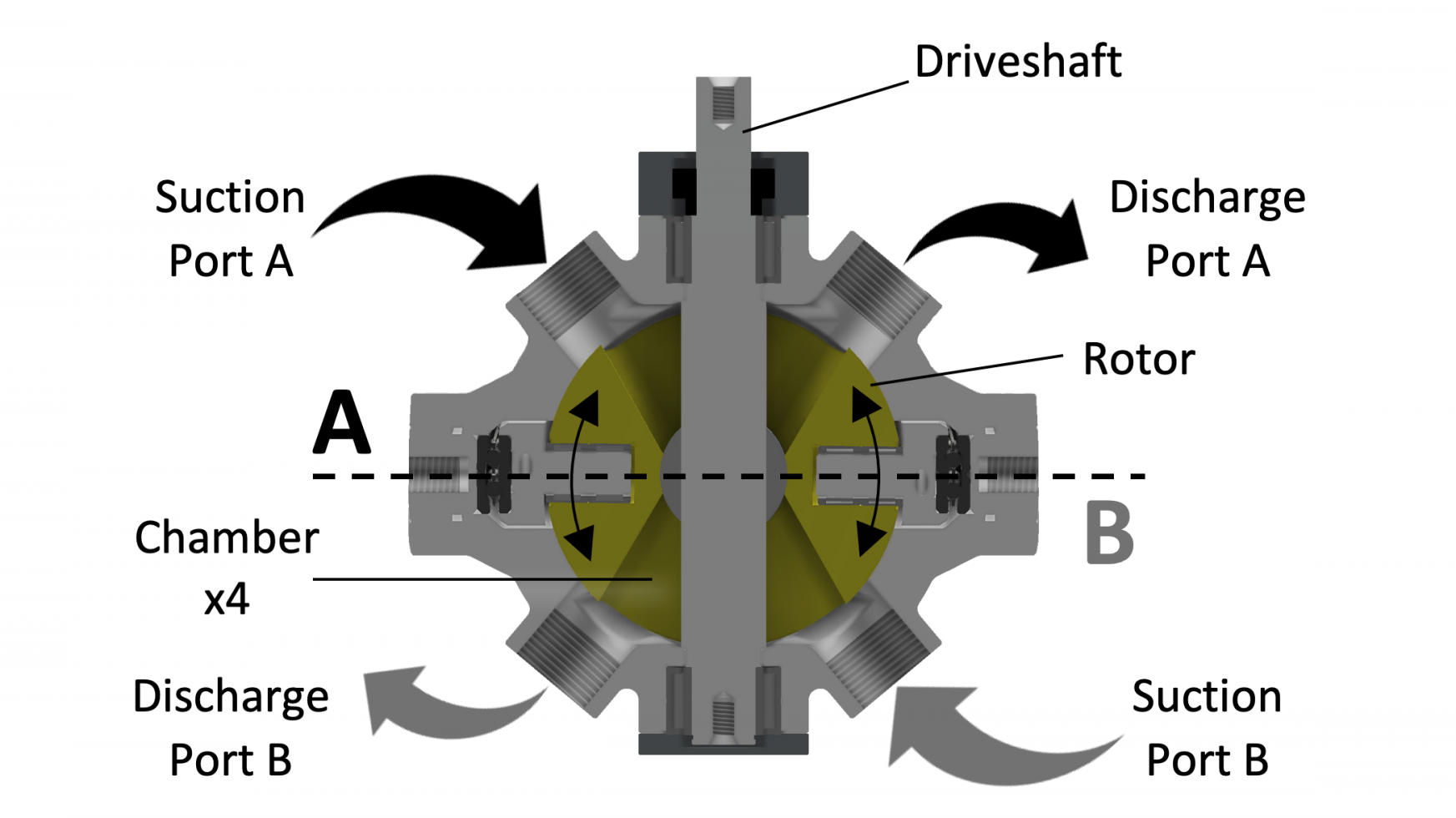
Mechanical Overview
Roticulation can outperform technically complex machines which utilise many hundreds of parts (a car engine being a good example), yet itself has only two moving parts, consisting of:
- A drive shaft - which delivers or extracts shaft power from the rotating internals.
- A rotor - linked to the drive shaft it simultaneously rotates and articulates in a predictive and controllable fashion. The rotor oscillates in such a way that two pairs of anti-phase chambers systematically expand and collapse, provisioning absolute chamber evacuation.
The design describes four discreet positive displacement chambers arranged in two double-acting pairs, enacting the complete cycling of the four chambers in one 360° revolution. Ports in the outer casing allow for controlled entry/exit of fluid media, the rotors proximity at the appropriate phase negates the need for valving. The seamless presenting of the subsequent chamber enables the device to operate in a continuous fluid manner (akin to a turbine) and high built in volumetric ratio providing an exceptional degree of efficiency. Its chamber walls do not make contact and offer no potential for wear or inefficient friction.
Test and Validation:
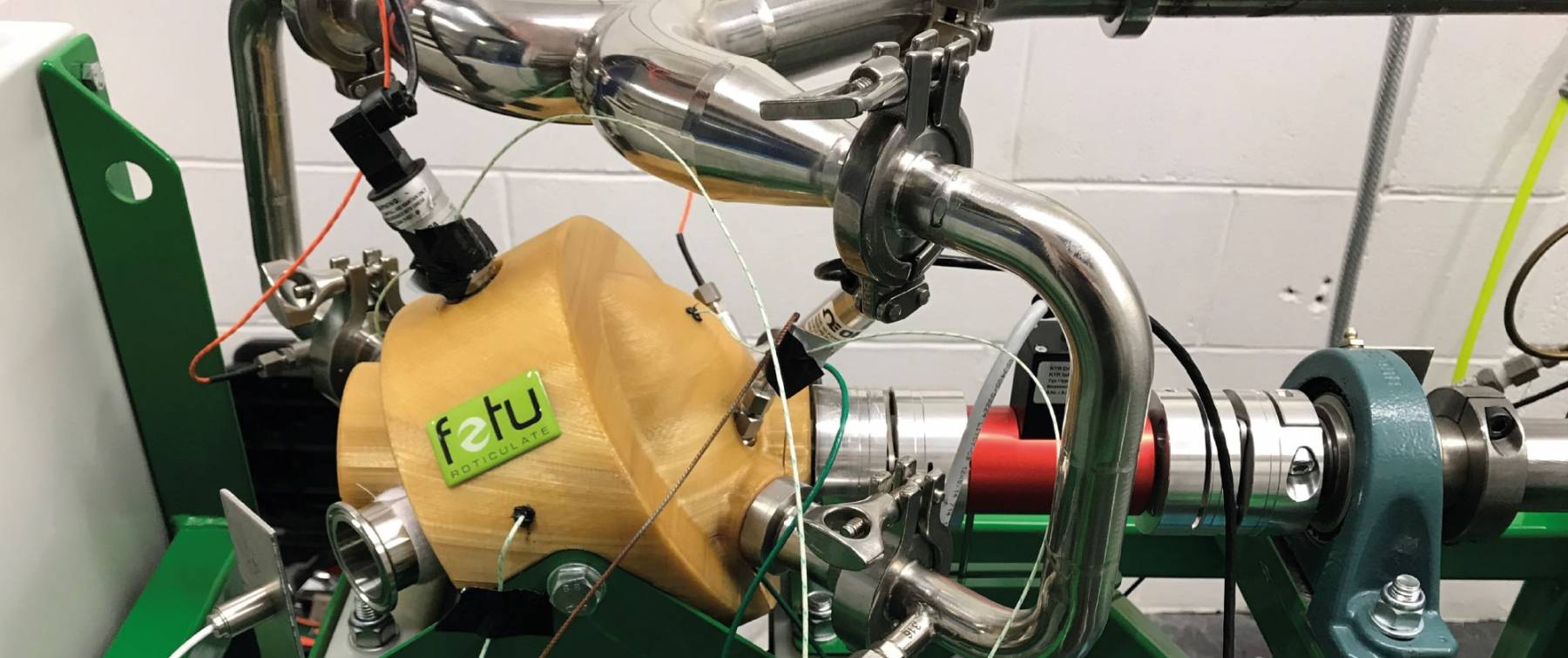
Testing of Evolution II was completed in collaboration with the University of Bath. The FeTu device was run within a compression cycle and a vacuum cycle. A Paper has been written on test findings and was presented at the 11th ICCS 2019 event:
THE ROTICULATING CONCEPT AIR COMPRESSOR: EXPERIMENTAL AND NUMERICAL INVESTIGATION
The aim of this was to take the concept from TRL 3 to TRL 5. A variable-speed test-rig was designed for the FeTu concept to allow pressure, temperature, torque and mass flow data to be captured as a continuous-flow process using a data acquisition and control system, recording a wide range of pressure and speed conditions.
TEST RIG DESIGN
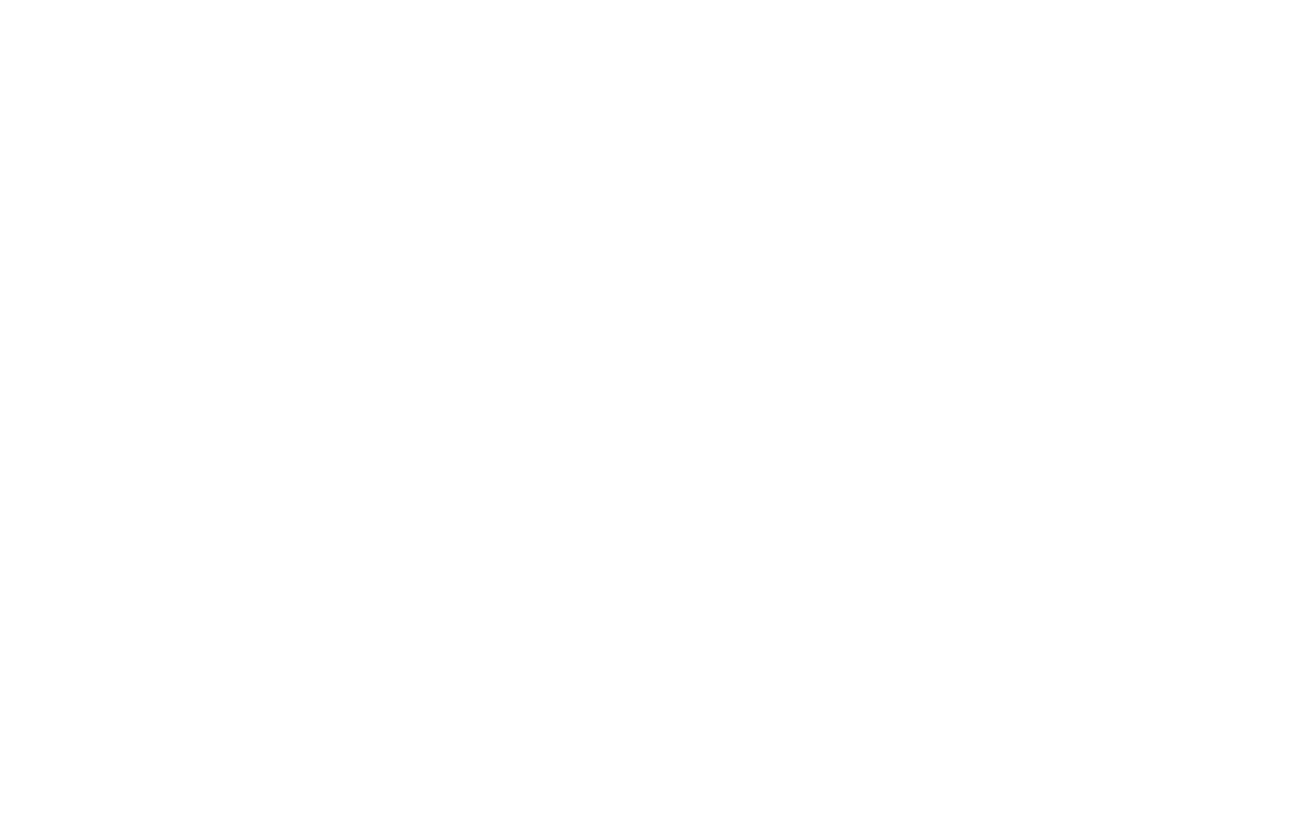
A FeTu unit is fitted to the test rig, fully instrumented, leak-tested and lagged. Tests typically start with the gate valve fully open at 100 rpm, data is captured after system stabilisation then the pressure is increased via the gate valve, stabilised and recorded at the new pressure. A full range of pressure ratios are collected before the gate valve is fully opened, unit depressurised, and the speed indexed by 100 rpm. This process continues to up to 1500rpm. Therefore, there is a wide range of performance data at different pressure ratios and speeds.
Variations in clearance, NRV cracking pressure and the addition of contact seals were explored in pursuit of an optimal configuration to maximise volumetric efficiency and performance.